The aim of a modern shipbuilder is to build better ships, to constantly improve designs to fabricate vessels that are more efficient, more effective and more sustainable. This is what shipbuilders’ clients demand. For a naval shipbuilder like Damen Naval, with vessels in active service all around the world, clients have even more specific requirements.
“In recent years, we are seeing that naval clients want their ships to be faster, lighter and therefore, more slender,” begins Damen Naval Senior Structural Analyst Alejandro Luna García-Valenzuela. This trend marks a change from what can be considered as the more traditional designs. “In general, naval ships used to be ‘over designed’ – this made them heavier and stronger. These days, clients want the best of the best. Lightness means that you can load your ship with more functionalities. And speed allows you to reach any point on the planet as fast as possible.” Building more slender naval ships is the most obvious way to achieve speed and weight reduction, but there is a challenging consequence to these design demands. “The faster and lighter a ship is, the more significant the issue of fatigue becomes. The length is also a critical aspect: a fast and light ship that is only 20 metres long will not have many fatigue issues, whereas a fast and light ship that is 200 metres long will have plenty of fatigue problems.”
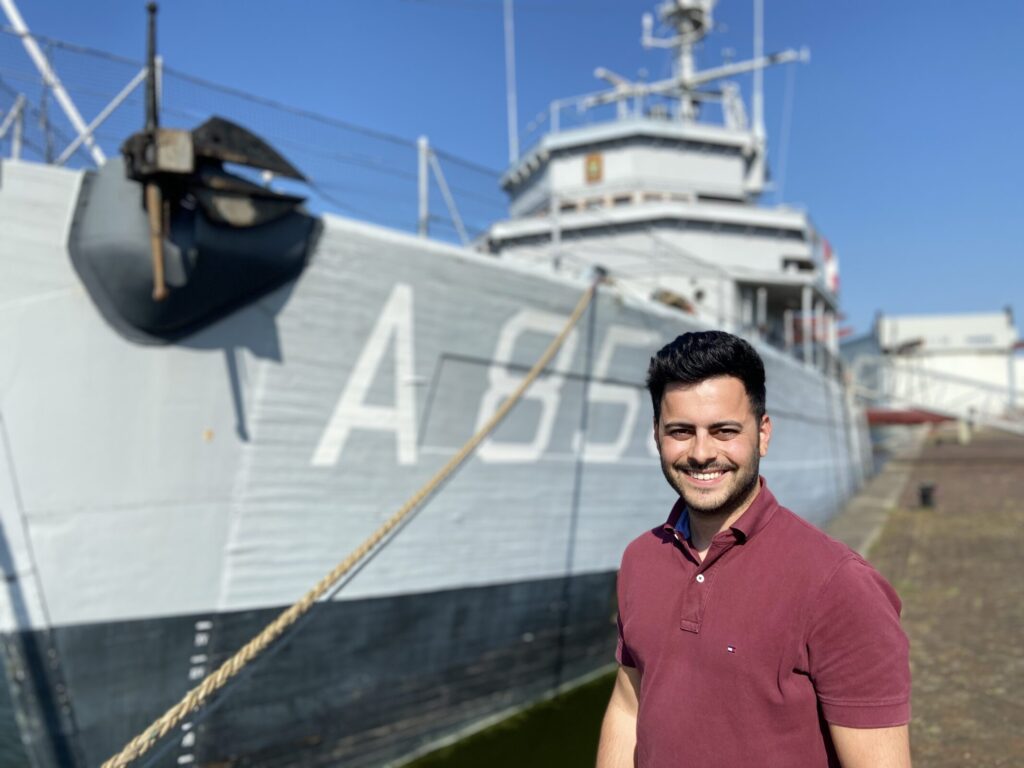
Damen Naval’s R&D activities target the innovations rising from the evolving demands of its clients. This is where Alejandro’s field of expertise comes in; since starting at Damen Naval in 2019, as well as working on the engineering teams for various projects, he has been specialising in ship fatigue. More specifically, “working on new methodologies and technological tools to solve fatigue lifetime calculations”, he says. He divides the complex subject of ship fatigue into two different scenarios. “First is the incoming load, which is caused by passage through the waves. The second part is the ship’s structural response, how the ship deforms against the load,” Alejandro explains. The effects of fatigue, however, are singular. “Fatigue can trigger the formation of cracks at structural welds and at surroundings of big openings; this may reduce the capacity of the structure against further load scenarios.”
“The faster and lighter a ship is, the more significant the issue of fatigue becomes." Alejandro Luna García-Valenzuela
The main part of Alejandro’s research into fatigue started when he was working on his Master’s thesis during his internship at Damen Naval. Working closely with his then supervisor and Damen Naval Principal Structural Analyst Izak Goedbloed, the aim was to couple these two aspects of fatigue (the pressure distribution over the hull and the structural response) more efficiently. “This had been done previously, but only manually; we wanted to improve the efficiency by automating the fatigue assessment.” He achieved this by developing a dedicated software tool – called SEAFALT – to perform the automated fatigue calculations. After presenting his Master’s thesis, he continued developing and improving the tool to create a version ready for release.
“With SEAFALT we not only can automatically assess fatigue performance of the ship, but also with increased accuracy.” SEAFALT – which stands for Long-Term Spectral Fatigue Analysis – was tested using a full-scale detailed Finite Element model of an 85-metre-long Damen-built pontoon discretized with a cloud of more than 256,000 structural nodes to accurately assess simulated fatigue patterns.
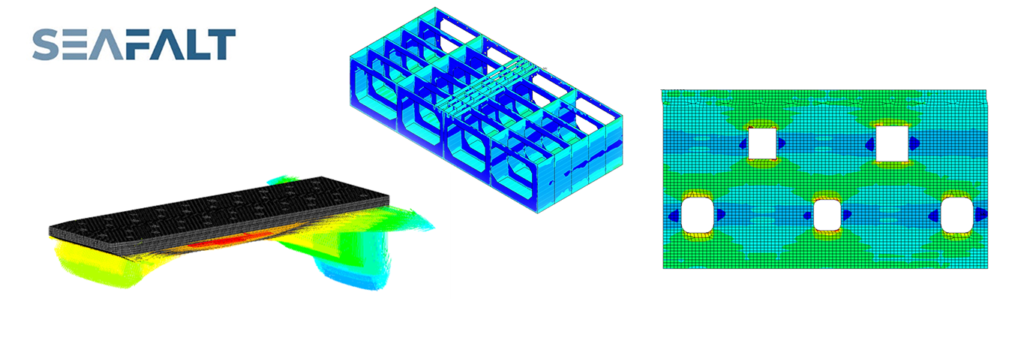
Alejandro describes the early version of SEAFALT (developed in 2019) as “more of a theory-based engineering approach”. In 2023, however, he says that “the intention is now to get it more involved in the engineering process”. To that end, SEAFALT can be used to help clients predict how their ship is going to behave in terms of fatigue. “This spectral fatigue analysis looks at the variety of predicted sea states that the ship will be operating in during its 30-year lifespan,” adds Alejandro.
In addition to using SEAFALT during the design phase, this Damen Naval R&D programme is also working on applying it to the operational phase of a vessel. Alejandro: “Instead of predicting fatigue that will happen in the future, on board sensors will provide the ‘live’ scenario. This is called the ‘structural hull monitoring’ concept where the full sensorisation of a ship gives us a huge amount of data regarding stress and deflections. We can use these data and the SEAFALT methodology to actually measure the amount of fatigue lifespan consumption or damage.”
Such ‘real-time’ structural assessment is a step towards smart maintenance. “This is predictive instead of corrective maintenance, also called CBM, Condition-Based Maintenance,” notes Alejandro. “We want to be able to advise our clients whether their ship needs to go to dry dock or not. Another possibility is condition-based operations; how can I operate my ship depending on the current status of the structure. National and international naval clients are really interested in this technology for their future ships. Moreover, this is going to impact commercial vessels as well as naval vessels. Therefore, we are building a nice synergy with the RD&I activities at other companies within the Damen Shipyards Group.”