Proper maintenance of your own equipment is a fundamental aspect of safe and effective operations for any shipyard. For Damen Shiprepair Vlissingen, 2023 has called for the renovation and overhauling of two crucial items of equipment.
The first project has been the maintenance of the dock door at DSV’s dry-dock number 1. The scope of work began by ‘floating out’ the dock door from its position at the end of the dry-dock on 7 June. An important starting point: the water level in the dry-dock has to be the same as outside the dock.
DSV’s Maintenance Coordinator Lennard Sturm outlines the dock door removal process: “By adjusting the levels in the internal air chambers and water tanks, we start to float the dock door. At a certain point, we lean it outwards on its hinges to a 40-degree angle. From this position, we can float it to the surface of the water – at this point, it looks a bit like a pontoon,” says Lennard. A notable point about this whole process is that, even though the dock door weighs approximately 200 tonnes, it only takes about 30 tonnes of lifting capacity to lift and manoeuvre it out of position, thus highlighting the purpose of the internal air chambers.
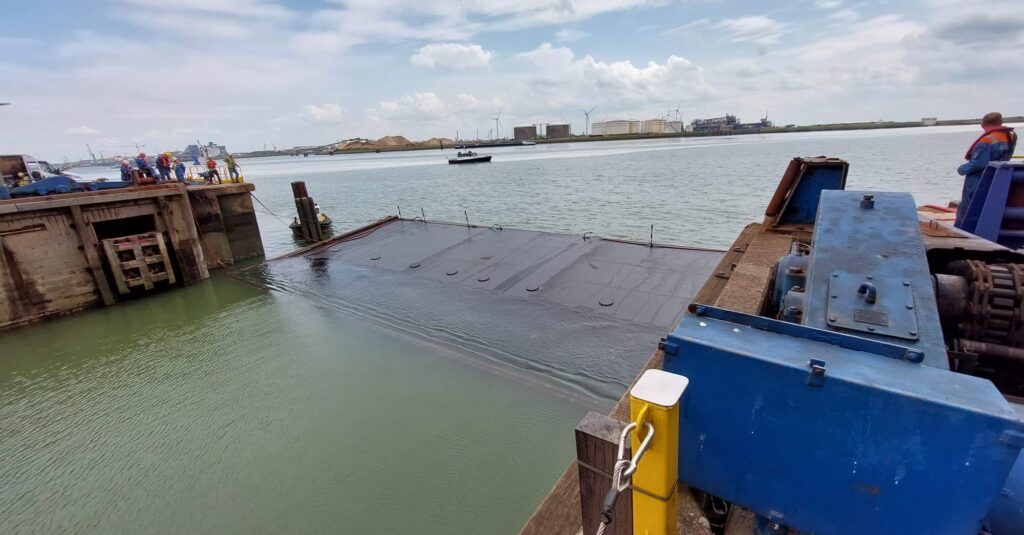
Once floated, the DSV team (under the watch of Project Manager Wim van de Velde) transferred the 26-metre by 10-metre dock door the short distance to dock #2, where it could be worked on in dry conditions. According to Lennard, compared to the previous dock door maintenance job (in 2021, the dock door from dry-dock #2 required the removal of no less than 55 cubic metres of marine fouling such as barnacles, shells and seaweed, read more about that here) the condition of the dry-dock door #1 was actually not that bad. “There was minimal marine growth which meant that we could quickly get to work on replacing the zinc anodes and sandblasting and painting the whole structure. In addition, we replaced the vertical wooden side beams and their rubber seals.” Following a smooth work process, the dock door was returned to its original position on 20 June.
The second project involves the maintenance of one of DSV’s mobile harbour cranes. “We have three harbour cranes here at DSV,” says Project Manager Bas de Klerk. “We could see that one of them – the 40+ yearold Takraf that we purchased in 1991 – was in need of an overhaul. And when we started discussing the project, we quickly came to the conclusion that this would be a comprehensive overhaul – we want to set the crane up for another 15 to 20 years of operations.”
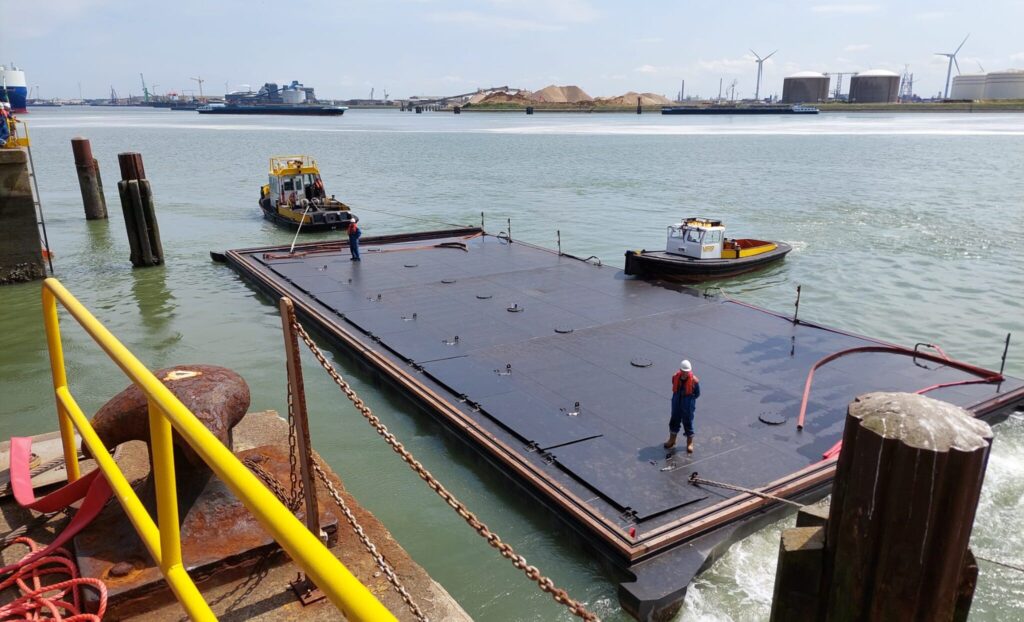
Starting in May, one of the first things to do was to remove the crane’s 86-metre long and 26.5-tonne boom, a task that was carried out by two contracted mobile cranes. The DSV team then transferred the boom to the covered conditions of dock #2 for much-needed steel repairs, blasting and painting. The crane’s engine room remained in place, approximately 35 metres high, where work began on disassembling all moving parts. “This included the hoisting winches, gearboxes, the controls – apart from the winch spools, we took out most of the engine room,” adds Bas.
There is one particular aspect of this crane maintenance project that is very similar to DSV’s core business of repairing ships. “Yes, the hidden surprises,” says Bas. “You know that you are going to find them in a job like this, but you’re not exactly sure where and when. This crane’s gearboxes, for example, you know that there will be some wear and tear, but until you open everything up, you just don’t know how bad it will be.” Consequently, the project has required a considerable amount of new components such as bearings and (fitting) bolts.
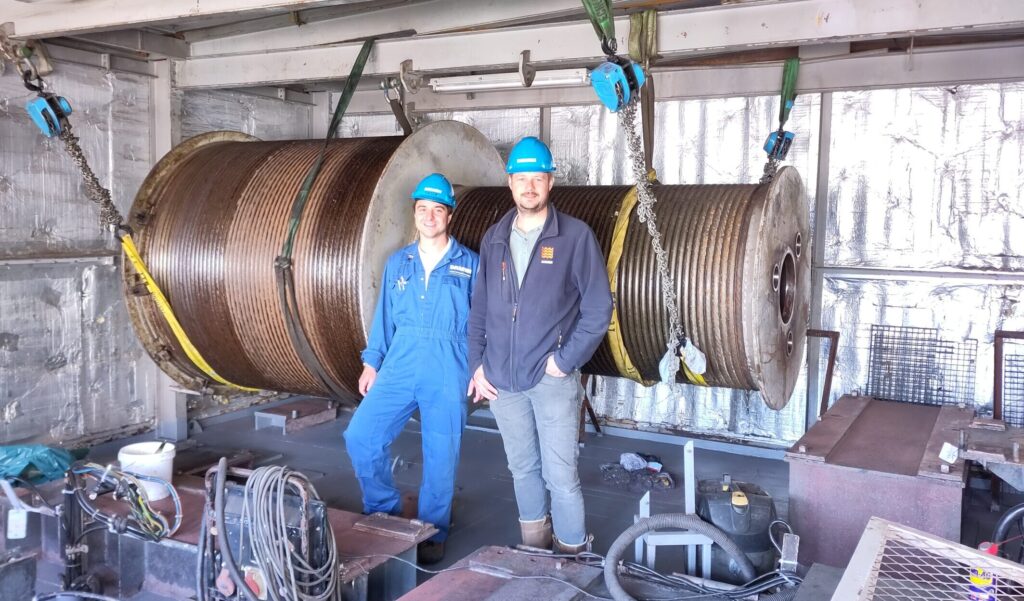
The Takraf crane maintenance project is due for completion at the end of the summer. At that point, the covered scaffolding will be removed to reveal a fully renovated mobile harbour crane, freshly painted to match the blue and white of DSV’s other cranes. As such, as well as being newly certified, the crane will look as good as new. “The painting is an important part of the job – after all, these cranes are like our business cards,” notes Bas.
Lennard adds that both projects called for the close coordination of numerous teams at DSV. “These in-house maintenance projects involved teams from maintenance, steelwork, the docking team, work preparation, and the fitters department. Therefore, these two projects are a real example of the teamwork that we have here.”
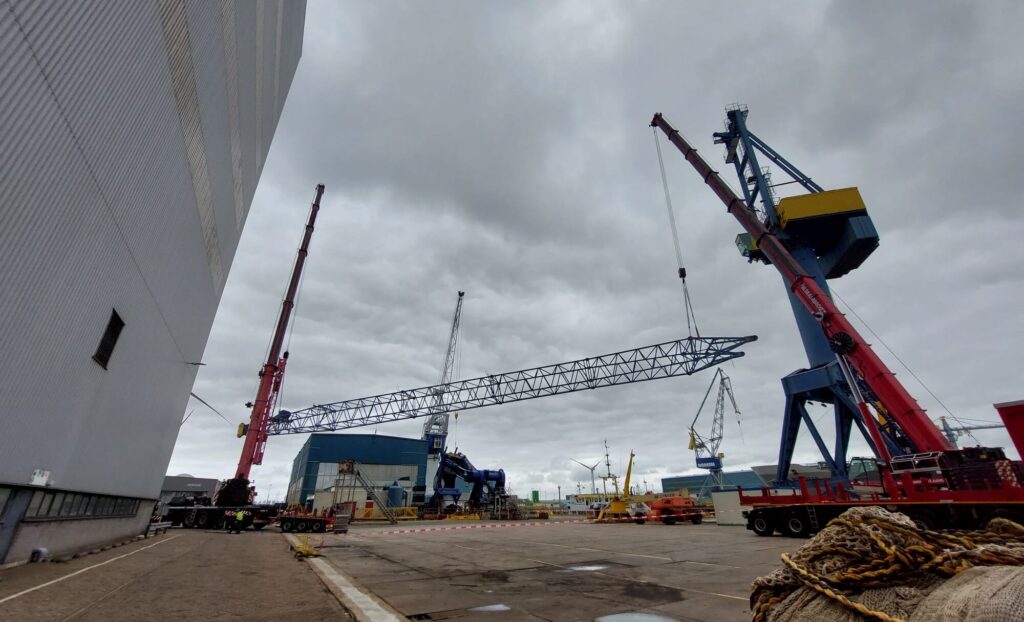