Damen Naval’s F126 project is huge in so many ways. From the number of people working on it (~400), the number of messages to the client so far (12,000+), to the number of requirements (~10,000). It consists of six Teilprojekten (sub-projects), each of which is large enough to be a standalone project by previous Damen Naval criteria. It also involves several aspects of project management that Damen Naval has not (to such an extent) implemented before: risk management, systems engineering, security, requirements management, verification & validation, and change management. With first steel-cutting scheduled for December 2023, Project Director Frank Verhelst and Commercial Director Magiel Venema give the ’big picture’ view of the F126 project.
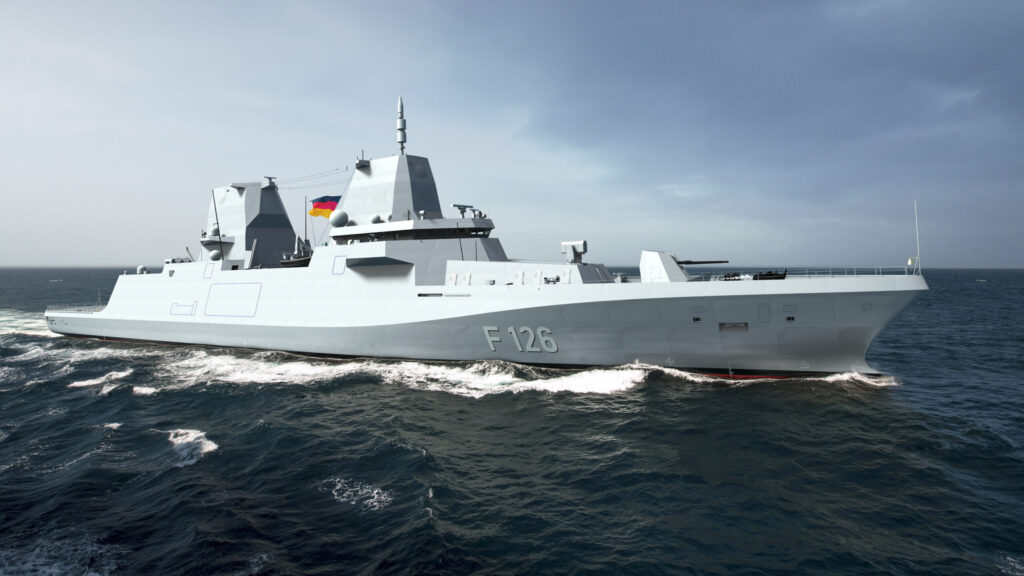
What is the current status of the F126 project?
Frank: “During the first three-plus years of the project, I am pleased to say that we have met all our contractual and financial milestones with our client. Just before the summer, we reached the huge milestone of the Critical Design Review for the combat systems; this called for intense corporation with Thales.”
Magiel: “Besides our visible milestones, we have many other internal – less visible – milestones too. The FATs [factory acceptance tests] of the main equipment like main engines, electric motors, and switchboards are a good example of these. These will all start in the coming period; in fact, the main engine FAT has started already. The FATs mark the point in the project where we can finally start to see and touch things. Ideas are starting to be transformed into steel and electronics – it is becoming extremely exciting.”
Who is involved in the Factory Acceptance Tests?
Frank: “The FATs are important because so many aspects of the project are coming together: people from quality, purchasing, and requirements management, for example. It is a dynamic period because it is happening at our suppliers’ factories in Europe and around the world. And of course, the client is closely involved with the FATs.”
Tell us more about working with a German client. Are there any culture differences?
Frank: “We [the Damen Naval team] work very much on the principle of planning the first 80 per cent of a particular element of the project. The remaining 20 per cent? We’ll cross that bridge when we come to it. The German way of working involves planning every aspect of the subject to 120 per cent before you actually get started. Although these are two very different ways of working, both Damen Naval and the client realise that we can learn a lot from each other. What’s more, we have intentionally included a significant number of Germans on our own project team. This has given successful results; we really appreciate our German colleagues on this project.”
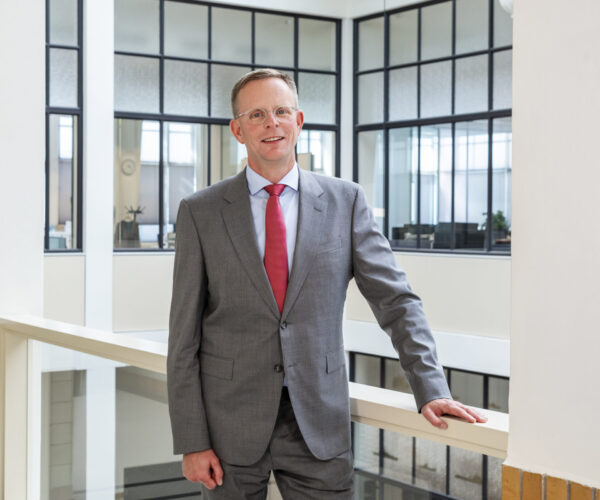
Magiel: “Investing in our relationship with our client BAAINBw is very important. This is shown as an example on the ‘Info Tour’. This is a first for Damen Naval, during which Frank and Bertram Liebler [deputy F126 project director] will accompany the project management of the client during visits to key stakeholders of the client. The purpose will be to inform the stakeholders of our status, the upcoming milestones, the challenges we face, and to connect them. This is a real joint effort with our client and is a very good example of our project motto: unser gemeinsames Ziel (German for: our common goal).
“Moreover, at the end of September we were present at the Marineworkshop naval conference in Linstow, Germany where among others the commander of the German Navy visited us. I won’t go so far to say that we are an established part of the German maritime establishment, but we are getting there. This is a sign that we are getting more and more accepted – becoming part of the German naval industry ecosystem.”
How many people are on the F126 team at the moment?
Frank: “We are close to 400 people booking hours every week, working in Vlissingen, Schiedam, Hamburg and MEGA in Romania. In terms of team size, we are at our peak. This is why we are investing a lot of time into team building and communication. Besides the technical aspects of the project, the human element is crucial.”
The F126 team works in a highly secure and restricted environment. What challenges does this bring?
Magiel: “I don’t see this necessarily as a restriction. It is an adaptation – and we have to adapt to this new reality. Every project that Damen Naval will work on from now will surely be in some sort of restricted environment. This means that, in many ways, this is a groundbreaking project. We are working with new rules for security, new software, and new methods of project information management. Yes, it’s new, but from now on, many elements will be the standard. We are the forerunner. In an ideal world, maybe we should have started this new way of working on a smaller, less complex project. But then maybe we would have been tempted to postpone certain actions and innovations. Any change causes headaches, but if we don’t do this, then I see the risk that we will run into obsolescence.”
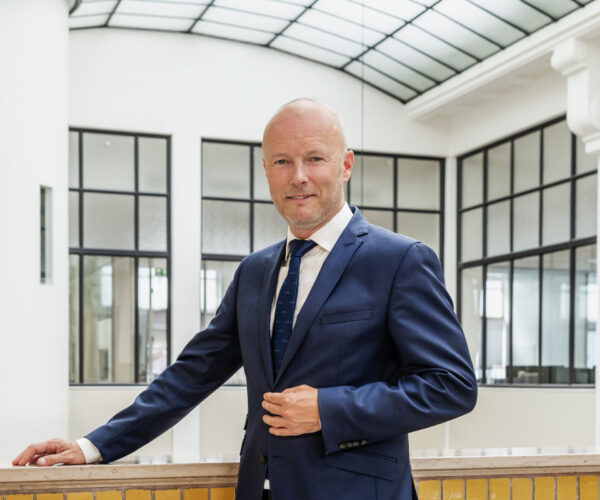
On the subject of this ‘new way of working’, we understand that you have been informing other Damen companies of this?
Frank: “Yes, I have been to Damen Yachting, telling them of our experiences in a way that we can share our lessons learned. I explained the ‘hows’ and the ‘whys’ of the F126 project, as quite a lot of things that we are doing on this project will be translated into new projects. This includes new software, processes, and information management. To that end, I am convinced that 3DX is a highly professional platform that fits our projects, for now and in the future. It also includes requirements management, change management, project management. This consists of a lot of change – and change always has an impact. But this reflects the larger changes that we are working on as a company.”
So, what is next for the F126 project?
Frank: “After our extensive project preparation and engineering period, we will be cutting the first steel for the first F126 frigate in December. This is, of course, a major milestone. Just like other Damen Naval projects, the engineering will continue in parallel with production, aiming to deliver the last production information at the end of 2024. Another upcoming milestone will be keel-laying which is planned for the first half of next year. So, we have a few exciting milestones to look forward to.”