Blowing helium-filled soap bubbles over and around a 1:70 scale model of a Dutch Navy OPV in a wind tunnel; filming the process with six cameras; analysing the results with cutting edge software: these are the key points of Damen Naval’s latest industry collaboration. The purpose of the research? To gain a deeper insight into the effects of wind and airflow on the performance of frigates.
Eric Roosenboom, from the Naval & Technology department was the Damen Naval contact involved in the research, which took place in December 2023. “We collaborated with the Royal Netherlands Aerospace Centre, COMMIT, DNW German-Dutch Wind Tunnels, and software developer LaVision to carry out these low-speed wind tunnel tests on a model of a Holland Class Ocean-going Patrol Vessel,” he says.
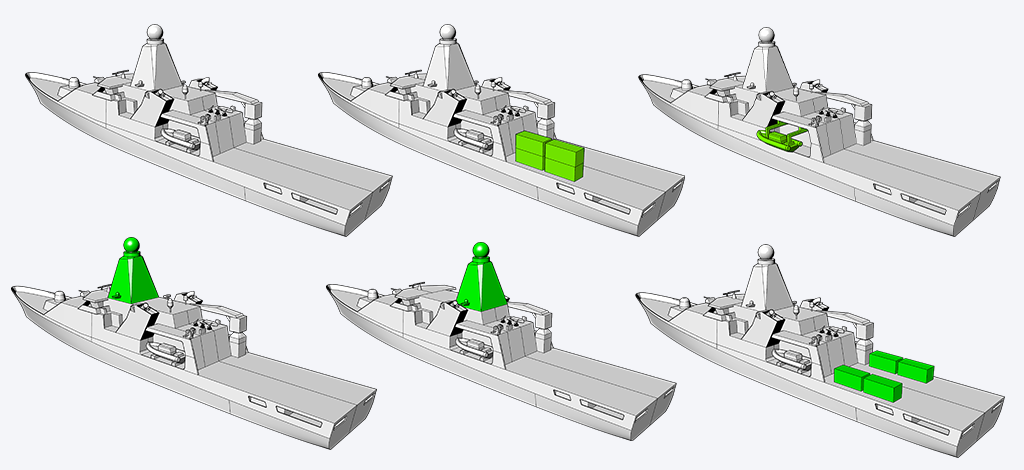
The method used marked a ‘industrial first’ for all participants. “We used a new flow measurement approach where we employed an omni-directional particle tracking velocimetry setup using helium-filled soap bubbles,” explains Eric. The small helium-filled soap bubbles have the same density as air and therefore accurately follow the air flow. The bubbles are illuminated with lasers from four directions and filmed with six different cameras. A vital part of the research was the analysis software that had been developed by LaVision. “They supported the research to make this technique possible – their dedicated software gathered air flow measurement data from all around the ship model,” notes Eric. “This was the first time that we have been able to measure the complete air flow field – which includes both turbulence and changes in velocity – in 3D around the complex structure of a frigate in an industrial wind tunnel.”
Working closely with the Dutch Ministry of Defence, Eric determined a number of operational and design case studies that would be most applicable for the wind tunnel testing.
From an operational point of view wind tunnel testing is needed to determine so-called Ship Helicopter Operational Limits (SHOL) which “look at the conditions under which a helicopter can safely land or take off from the helideck” continues Eric. With future developments, similar evaluations will be required for drone launching operations, the technical term of which is the Ship UAV Operational Limits (SUOL). “Drones are most commonly launched from the helideck. They can also be sensitive to fluctuations in wind,” explains Eric.
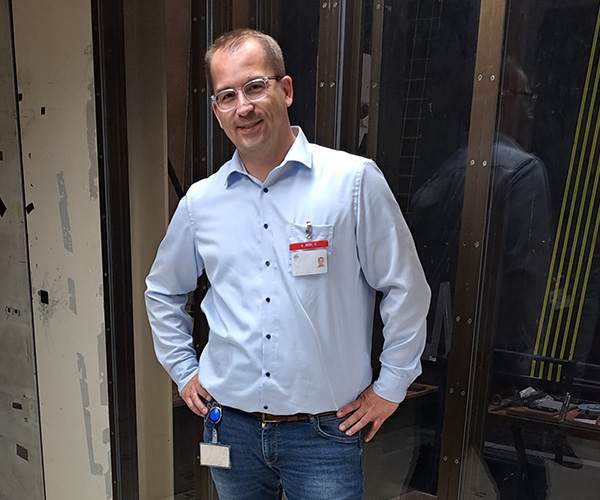
The first operational case study took a closer look at drone launching operations. “Because all the associated drone equipment and controls are kept in a container which is also placed on the helideck, we thought it would be interesting to look at the possible wind disturbance caused by those containers.” With this in mind, wind tunnel testing was carried out with different container positions: two on port, two on starboard in addition to four containers on one side. Other operational case studies investigated the effects of various other activities on the SHOLs and SUOLs This included the effect of extending a RHIB over the side of the vessel.
From a design perspective, the position of the mast affects the velocity and turbulence at the helideck. “Therefore, we placed the mast in various positions, moving it forward and aft of its existing position as well as having no mast,” he says. “This will be useful information for future frigates.”
The research represents an important cooperation with the Royal Netherlands Navy. “This wind tunnel testing gave us valuable insights in how wind speeds and directions can influence the performance of the vessel. The results of the measurements will be used for the further development of frigates as well as to provide more details on the operation of drones from a helideck. As such, this research was very worthwhile for our main client. For us, tests like these are not only very interesting for us a ship designers, but they help us deliver better products and improve existing vessels,” concludes Eric.