After a brief mention in the previous edition of the Schelde Schakels, it is now time to take a closer look at Damen Naval’s STEP programme. STEP – which stands for Sustainable Tooling & Enhancement Programme – is a new initiative with a focus on improving the processes, tooling, and training materials within the company. It is, therefore, inherently linked to Time for Change, says STEP Programme Manager Onno Spoor. “As a company, we are making changes to future-proof our organisation. STEP is part of this.”
STEP has two main areas of attention: the F126 and ASWF projects. “We envisage improvements to tools, processes and training first being implemented on the F126 project, but also making sure that these are usable for ASWF,” explains Onno.
Organised by a steering committee consisting of people from the MT, F126 and ASWF teams, STEP currently involves around 50 people working part-time on different subjects. “We have separate teams working on IT performance and 3DX, for example. There is also a team from Dassault [the software provider of 3DX] that is working with us on the acceleration of 3DX.” Although Onno describes 3DX as a “big player” in the STEP programme, it is by no means the only software tool that could benefit from efficiency gains. “3DX is about 75 per cent of the landscape that we are working on, with other subjects including Power BI, S-Tools, and a portal for co-makers and suppliers.”
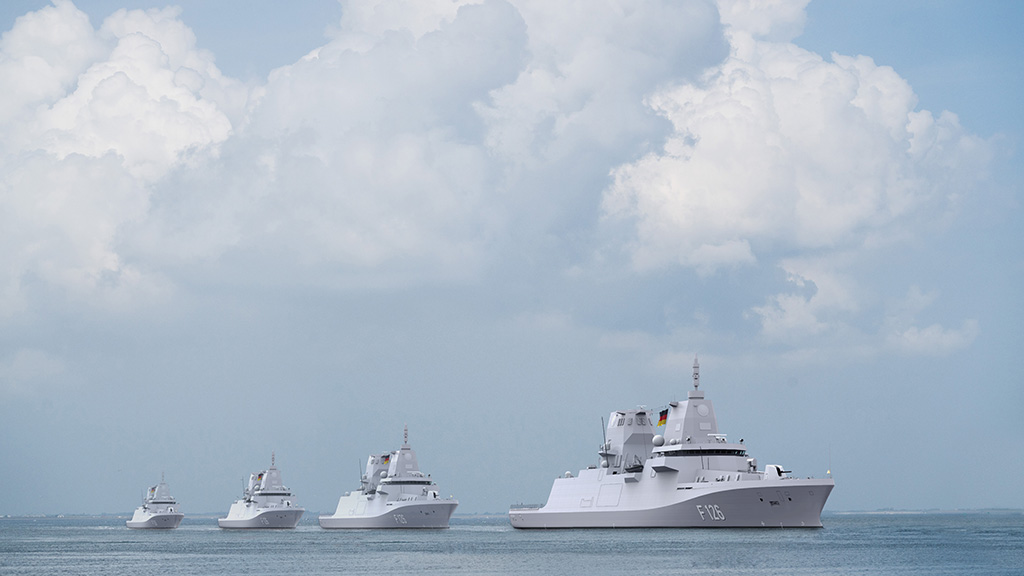
The working methods of STEP will first identify the key questions facing project management. “We are going to have a committed look at the processes: are they in place? The tooling: is it implemented? Are there any performance issues with the tool? Are there training materials available? This will give us insight of where we are now, what we have under development, and what we need to work on,” says Onno.
Onno is aiming for the first results of STEP to be visible around the summer of 2024. “We are working with a six-month time frame,” he says. “We want to raise our efficiency levels to around 80 per cent. We are going to achieve this by shifting gears on a number of aspects; by resolving process or performance issues, or introducing a piece of tooling if not available.”
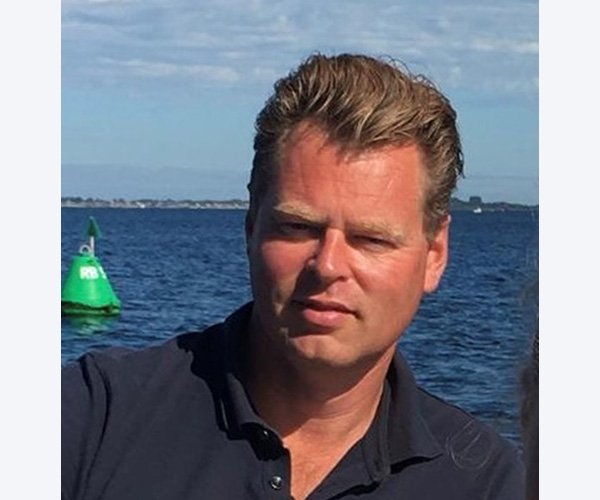
Measuring this 80 per cent increase in efficiency will be based on two very different factors. “Measuring efficiency is not an exact science. Yes, we have reporting functions in our project management tool Primavera which are very factual. But what I think is probably even more important is how people experience their work. We want to reach the point where people have more belief in the tools and processes that they are working with. We want to ensure that people are happier and less frustrated in their work.”
With this ‘human aspect’ in mind Onno describes STEP as a way to “refocus everyone’s attention”. He goes on to say: “We know that people are working as hard as they can. In fact, they cannot work any harder. Through the STEP programme, we will discuss the problems, the questions and the risks within the steering committee and then make decisions to prioritise the time of the team members. Some of those choices will be about what to do, and others will be about what not to do. STEP means deciding what topics we are going to focus on in order to increase the efficiency of our work.”