They call themselves the ‘engine oil’ of the ASWF project. Their job is to make sure that the design and construction of the new Anti-Submarine Warfare Frigates goes as smoothly as possible. In an interview with Senior Project Manager Engineering Sjaak Jan Jiskoot and Project Manager Engineering Richard van der Kolk, they talk about their role as project managers, team building, 3DX and the current state of affairs.
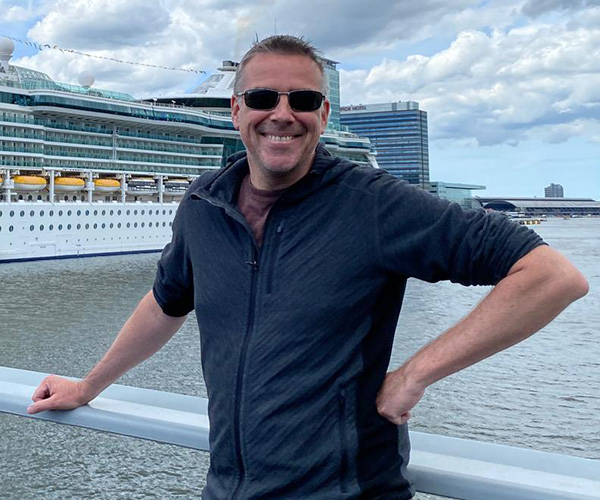
“In a lot of ways, we are lucky to be behind the CSS and F126 projects,” Richard explains. “We can check off what is going well and what can be improved, without having to reinvent the wheel.” For example, the ASWF project was split between Vlissingen and Schiedam. “In other projects, some colleagues sometimes felt a bit lost and disconnected from the rest of their team. That’s why we chose from the start to have a Team Lead and a Deputy Team Lead per team and one of the two is almost always present at each location.”
Sjaak Jan is mainly involved with ‘external’ operations; he maintains contact with the customer COMMIT, and secures the project requirements and takes care of their implementation. Richard deals more with internal matters: planning, the team and the project’s deliverables. “We chose to do it this way because of the size of the project. The basic engineering team already consists of 100 people and for detailed engineering at MEGA, we are also already growing towards 100,” Sjaak Jan says. “Of course, we want to add more people. We had hoped to incorporate some more people from the CSS and F126 projects, but as they are still needed there too, that didn’t work out. Therefore, we are now working with HR to find new people.”
The atmosphere on the ASWF project is very important to the project management. Therefore, meetings are organised regularly for the whole team where everyone is updated on progress. There are also team-building outings and fun ideas such as awarding a cake to the first person who manages to achieve certain project milestones. “That cake is then shared with everyone, which in turn helps with team bonding,” Richard adds. “We know every engineer and try to speak to everyone regularly. We provide space so they can contribute their ideas. I really see our role as the ‘engine oil’ of the team; as a supporting role so that our team can work at their best level.”
"I really see our role as the ‘engine oil’ of the team; as a supporting role so that our team can work at their best level.” Richard van der Kolk
The project is now preparing for the detailed engineering phase. “MEGA is already helping us in the basic engineering phase as well. With 3DX, the lines between basic and detailed engineering are blurring a bit,” says Sjaak Jan. “Instead of working with a basic drawing, we are now working with a 3D model, and we are enriching the database by putting in as much data as possible. This means that the role MEGA plays is changing somewhat. The goal is still the same: a detailed design, but the way we arrive at that design is different.”
According to Richard, the phases overlap each other more. He cites a separator as an example; the system that cleans the oil. “With the purchase of that system, we get all kinds of information from the supplier not only about the device, but also about the power and water supplies needed. These are things that used to be placed only in the detailed drawing, but which we can now upload immediately with 3DX.”
Sjaak Jan: “In 3DX, you can quickly see the actual model. It’s no longer just the main construction and the shape of the ship, but you can already see more defined spaces. We are still filling the 3DX library now, which is a long process, but it will save us time in the future. From the CSS project, we learned lessons about cable routing and piping, which is why we have already involved MEGA in pre-routing. This means that people from MEGA are already in the office in the Netherlands. This is necessary because we are working with a tight timeline, and we are pulling out all the stops to meet it. In early 2025, we will start cutting the first steel.”
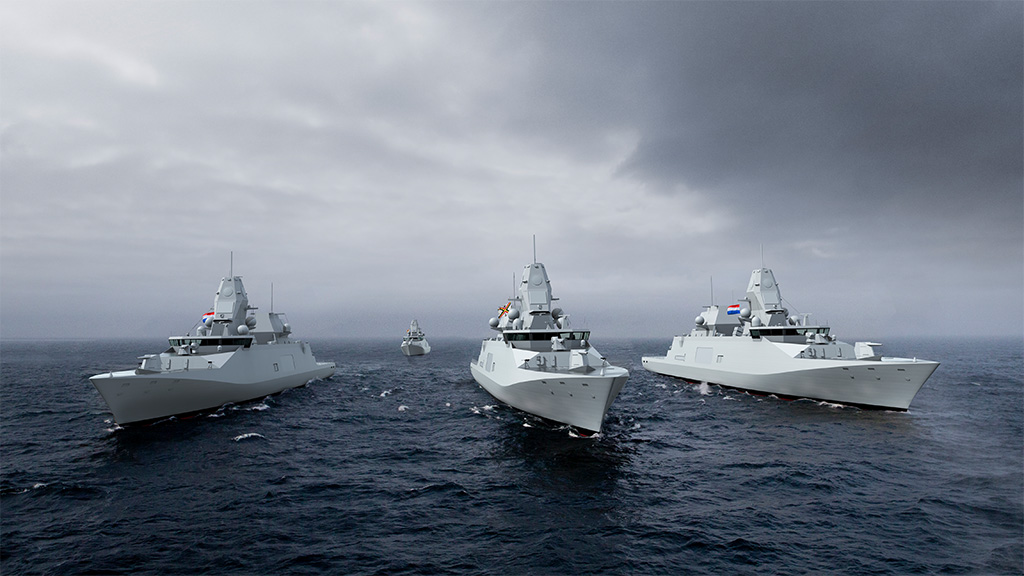
One of the spaces that is already largely complete in terms of engineering is the pump room. A lot of systems come together in this room: fuel and fire extinguishing systems, ballast systems, freshwater systems to name a few. “The teams have recently been checking whether all these components fit,” says Sjaak Jan. “The challenge on frigates is always that all systems, pipes, electrics and equipment have to come together in one space and that it is also safe to enter, that everything continues to function in the event of a shock impact and that the parts can also be maintained. We put a lot of time and manpower into setting up the space and we also involved Integrated Logistic Support (ILS) Project Manager Rens Melissen, for instance. ILS also looks at ordering the parts.”
Richard sums it up nicely when he says that on the project, it is like 100 people making a puzzle at the same time. “A huge amount of information is exchanged to make the puzzle as efficient as possible. The fact that we work in three locations adds complexity, but this is actually the most fun phase of the project. The info is in, the processes are clear, and we are enjoying working.”
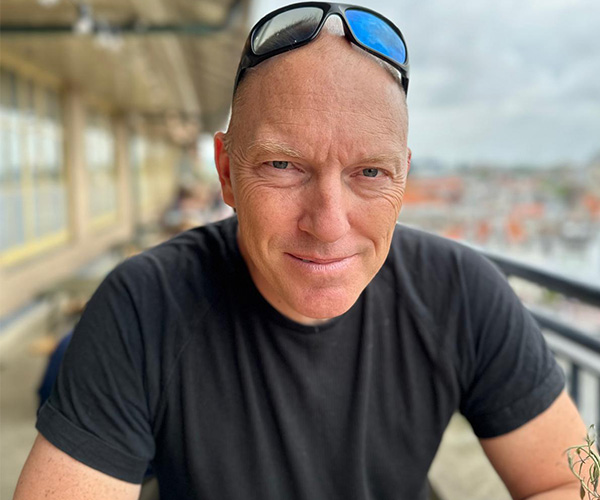
The relationship with customer COMMIT also plays a central role in the project, says Sjaak Jan. “From the beginning of the project, we have been working together in a different, closer way. With the office in Schiedam, we are closer to COMMIT and the knowledge institutes. COMMIT has its own space in the building where they can work with access to the floor where we work.” He says this results in a very open way of working with plenty of room for consultation. “We include each other in decisions as early as possible. By making the choices together now, we can later speed up the acceptance during the Verification and Validation procedures because everything meets the customer’s requirements.”
Damen Naval signed the contract for the design and construction of the ASWF in June 2023. The frigates can be used for multiple tasks, although the emphasis is on anti-submarine warfare. They are the replacements for the current Karel Doorman-class Multipurpose frigates. With the end of life of these ships in sight, the Netherlands and Belgium have decided on a joint replacement. Two frigates will be built for the Royal Netherlands Navy and two for the Belgian Navy. The first ship is scheduled to be delivered by Damen Naval in 2028.